The Requirements
To be a good fit for the Manufacturing Engineer / Continuous Improvement Engineer opportunity, you will have:- A bachelor's degree, ideally in Mechanical, Manufacturing or Industrial Engineering, or Production.
- 3 to 5+ years of continuous improvement experience in manufacturing environments.
- Deep understanding of Lean philosophies and tools gained through a combination of experience, education and/or certification. Quick question for you - click here
- Ability to teach/coach Lean methods to all levels in the organization and departments.
- Solid computer skills including MS Office applications (Word & Excel); ERP system(s) experience, ideally SAP (specifically relating to planning, manufacturing or material management modules); project management software. Quick question for you - click here
- Working knowledge of SPC techniques and process tracking metrics.
- Strong mechanical skills.
- Ability to work with Quality Management systems within manufacturing environments.
- Experience in machining environments highly preferred.
- Lean, Green Belt or Black Belt Certification preferred.
- Excellent leadership and interpersonal communication skills.
- Outstanding problem-solving skills.
- A team-player approach and the ability to interact effectively with all levels of the organization.
- Ability to manage a variety of cross-functional team members.
- Self-motivation and the ability to achieve goals with minimal supervision.
- The ability to manage multiple activities and priorities in a fast-paced environment.
- Flexibility and adaptability; a strong work ethic and drive to see projects through.
The Role
Reporting to the Manufacturing Engineering Manager, you will work directly with the Manufacturing Engineering team, including three manufacturing engineers, the hourly workforce and cross-functionally with all levels of management. The team supports machining and assembly processes for a variety of product lines, including pumps, valves, homogenizers and others. As CI Engineer, you will utilize Lean tools and disciplines to drive sustainable improvements in process, quality, safety and delivery. Quick question for you - click here
Your primary responsibility will be driving continuous improvements by identifying opportunities for improvements, doing investigations, Kaizen events, analyses, etc. You will also be involved with new product development, capital equipment justifications, cost analyses, business case development and more.
Specifically, you will:
- Support and champion team approaches to implementing continuous improvement change and solving problems working closely with plant management to achieve CI without jeopardizing safety, production or shipment commitments.
- Implement CI projects maintaining positive and productive relations, working cross-functionally with engineering, the hourly workforce, plant management team, and corporate representatives.
- Either directly or through teams, analyze Productivity, Maintenance, Safety, and Quality history and develop improvement opportunities using statistical analysis, machinery breakdown trends, quality failures, and other key process indicators.
- Analyze production floor layouts and identifying and implementing improvements utilizing lean methods such as value stream mapping.
- Schedule and lead problem-solving teams and Kaizen events with a focus on KPI and overall operating performance improvements.
- Work closely with manufacturing engineering and CNC programming to improve tooling and setup capability in our machining department.
- Manage track and lead projects to a successful conclusion.
- Perform administrative functions such as gathering cost information, developing project business cases, writing capital requests, reviewing and writing reports, and monitoring budgets and timelines.
- Estimates production times, staffing requirements, and related costs to provide information for management decisions.
- Confers with management, engineering, and other staff regarding manufacturing capabilities, production schedules, and other considerations to facilitate production processes.
- Apply Lean and Six-Sigma tools, methodology and philosophy in the implementation of business excellence initiatives.
Pictured: The APV® AP1 diaphragm valve range offers optimum protection of the product in aseptic applications. While this valve has applications in multiple industries, it features FDA and 3-A Dairy approval as well as European Hygienic Engineering and Design Group (EHEDG) certification, making it ideal for food & beverage and pharmaceutical production.
What's in It for You
Important, visible impactWe have structured our organization so that manufacturing engineers are the tip of the spear regarding continuous improvement. As our first fully dedicated CI Engineer, you'll take those efforts to the next level and serve as our subject matter expert. You'll also be able to move the needle in multiple areas, and anytime you can control costs and enhance efficiency, your successes will be noticed.
Professional development
There will be plenty to learn in the valves line alone, including different applications and multiple brands such as Waukesha Cherry-Burrell and APV. You'll also gain exposure to other products, such as positive displacement pumps, centrifugal pumps, heat exchangers, mixers and more. All this can position you to advance in our organization.
Autonomy and support
We're looking for a resourceful professional who can work with a good deal of independence. At the same time, you will partner extensively with others in achieving goals and resolving issues. In addition, your supervisor and colleagues in manufacturing engineering share ideas and insights.
Making a good thing even better
In 2015 SPX FLOW launch a global realignment program, involving structural changes and process enhancements to help the company operate more efficiently. We're also focusing on strengthening the diversity of industries we serve, such as promoting new product development within the food & beverage businesses. Q2 2017 results were very positive, with an increase in orders and operating cash flow, and reduction in net debt.
Excellent compensation
In addition to a competitive salary and bonus tied to manufacturing metrics, you will enjoy a comprehensive benefits package that includes medical and dental choices with costs shared by the employee and SPX FLOW; an employee-paid vision plan; a retirement savings plan with company match; paid time off; and more. Benefits begin day one.
Total Rewards
At SPX FLOW, what's in it for employees goes well beyond market-competitive compensation and benefits. Our Total Rewards program includes a comprehensive offering that combines a challenging work environment with opportunities for personal development, career growth and recognition. The program gives employees a financial stake in their own success and the ongoing success of the organization, and includes:
- Opportunities to be recognized and rewarded for hard work and a job well done.
- A platform to spotlight personal talent and achieve exceptional results.
- A chance to display the values and leadership practices we, as a company, embrace.
Keys to Success
Your technical expertise will be essential, but just as important will be your interpersonal and leadership skills. You'll rely on others to accomplish goals and implement change, so you'll need to be able to influence without formal authority. You should be a true team player adept at working well with others and communicating with stakeholders from shop personnel to the shop lead to plant leadership.In addition, in order to be an outstanding Manufacturing Engineer / Continuous Improvement Engineer, you will:
- Demonstrate skill at identifying gaps, finding solutions and converting solutions into action.
- Be organized and able to prioritize among multiple tasks, activities and deadlines.
- Internalize and apply given information.
- Support and promote a lean manufacturing culture from the production floor up.
- Bring initiative, energy and self-motivation.
- Get out on the production floor daily and remain willing to roll up your sleeves to get things done.
- Employ strong follow-up habits to ensure changes take root and flourish.
About Us
SPX FLOW is a global supplier of highly specialized, engineered solutions with operations in over 35 countries and sales in over 150 countries around the world. Our innovative solutions play a critical role in helping meet the rising global demand in the end markets we serve. Our total revenue in 2017 was $1.95 billion, with approximately 30 percent from sales into emerging markets.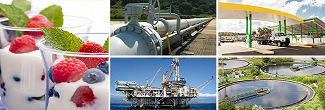
We focus on a number of operating initiatives, including innovation and new product development, continuous improvement driven by lean methodologies, supply chain management, expansion in emerging markets, information technology infrastructure improvement, and organizational and talent development. These initiatives are designed to, among other things, capture synergies within our businesses to ultimately drive revenue, profit margin and cash flow growth. We believe our businesses are well-positioned for long-term growth based on our operating initiatives, the potential within the current markets served and the potential for expansion into additional markets.